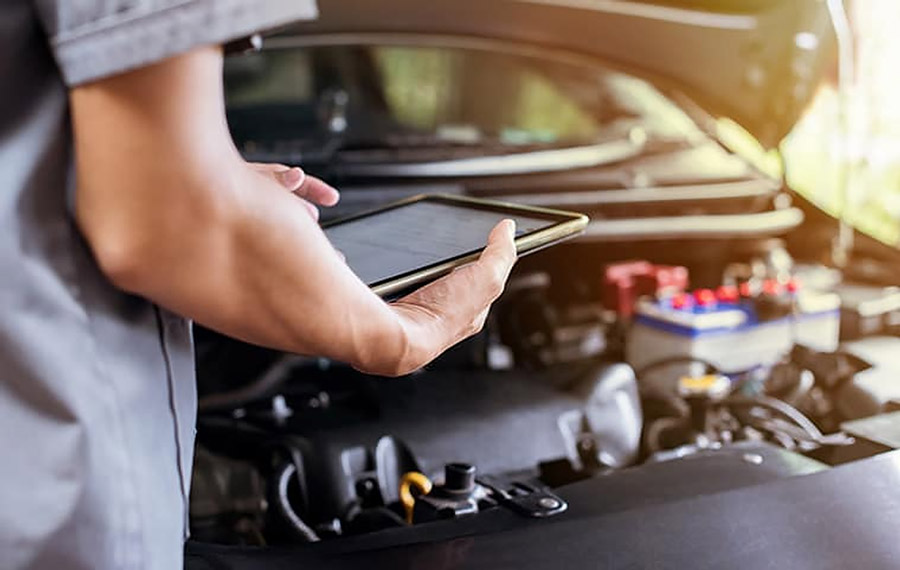
Work orders are a core part of fleet maintenance. Improving the work order process helps improve the efficiency of a fleet’s maintenance efforts. Fleet managers would be wise to optimize work orders at their company.
This article will outline what a work order is, explain the difference between “work order” and “work request,” and demonstrate how fleet managers can optimize their work orders with software. Finally, we provide tips on optimizing your company’s work orders with software.
What is a Work Order?
Work orders are the heart of a fleet’s maintenance operation. So what exactly is a work order? A work order is a document that includes all pertinent information about a maintenance task. It also outlines the process required to complete the job.
Work orders may include information on the job’s scope, who authorized it, the assigned technician, or expected results. These orders are integral to a fleet’s maintenance operation.
Work orders assist technicians and maintenance managers in prioritizing, organizing, assigning, completing, and tracking key jobs. Once completed, work orders help fleet managers capture vital information that is useful to improve efficiencies.
Know the Difference: “Work Order” vs. “Work Request”
Be mindful of the difference between “work order” and “work request.” Although they sound similar, they are distinct entities. Non-maintenance personnel may use a work request to alert the maintenance team of a task. In contrast, technicians use work order forms within the maintenance department.
For example, a driver might submit a work request when his or her vehicle needs a repair. A maintenance manager would review the work request, schedule the task, add any necessary extra information, and then assign it to a technician. At this point, the work request becomes a work order. Maintenance managers generally use a work order template to draft up work orders.
How to Optimize Work Orders with Software
Many fleets across the United States are still using paper to fill out work orders. Switching to digital work orders is the number one way for fleet managers to optimize their company’s work orders.
There are many downsides to paper work orders. They lack a record system, can be easily lost or damaged, and are sometimes made impossible to read.
Luckily for fleet managers, vehicle work order software keeps things optimized by analyzing vehicles’ operating costs and tracking service work (down to the line item). Vehicle work order software helps fleet managers to plan, schedule, and execute maintenance from start to finish.
Managing maintenance in one centralized software tool can help automate processes that will maximize your fleet’s efficiency. Automating vehicle maintenance saves time and money, and lets managers focus on more important jobs.
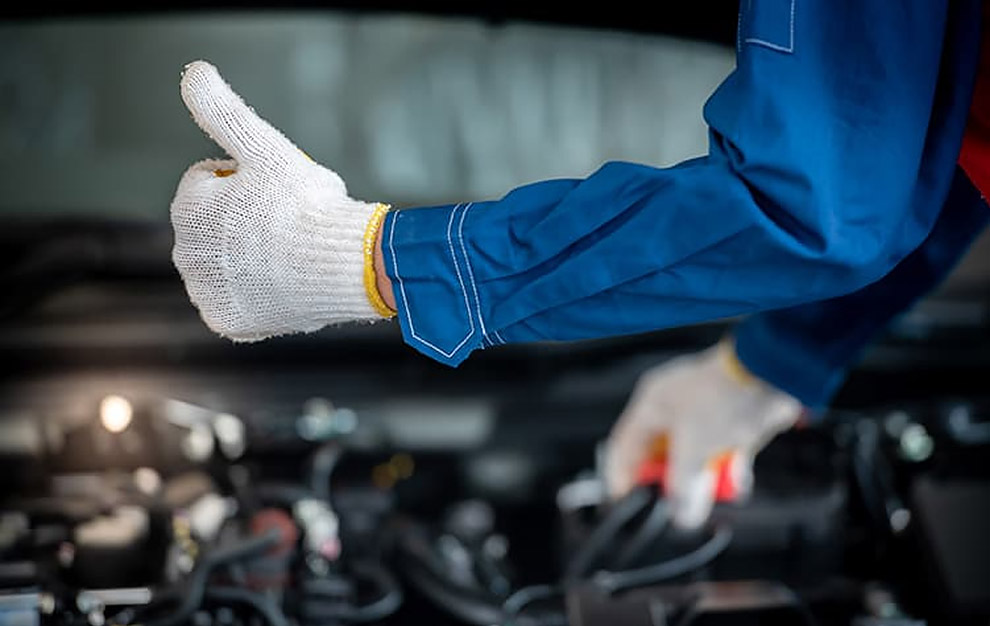
Tips for Optimizing Work Orders with Software
Plan and Execute Preventive Maintenance
A seasoned fleet manager knows that regular maintenance of fleet vehicles is vital. Vehicle work order software makes preventative maintenance scheduling easy. It gives fleet managers the tools they need to set service schedules based on drive time and odometer readings.
With vehicle work order software, fleet managers can receive mobile reminders of impending work orders. This simple reminder system helps them schedule routine maintenance of fleet vehicles in the shop.
Producing vehicle work orders based on preventative maintenance schedules lets fleet managers track parts and labor rates, and service progress. Such simple tracking gives managers a detailed look into their maintenance department’s total service costs and productivity.
Keep Tabs on Maintenance Resources by Line Item
Vehicle work order software lets fleet managers track line items for each service task. You can associate the cost of parts to specific tasks and include labor rates to track resources, expenses, and time spent. This tracking can significantly improve maintenance operations.
To complete service tasks effectively, fleet managers have to track maintenance resources down to the line item. Vehicle work order software makes it much easier to retrieve this data than searching through spreadsheets and receipts.
When fleet managers have a complete record of service in their fleet, they can connect diagnostic trouble codes (DTC) to line items. This data connection helps to make sure that their fleet has the most up-to-date understanding of their vehicles and can track issues as they arise.
Use Work Order Templates to Improve Workflows
Work order templates help all stakeholders spend less time creating work orders and make sure they are uniform and easy to understand. Vehicle work order software lets managers implement streamlined workflows that ensure their maintenance process is as efficient as possible.
A digital system is much more efficient than using paper work orders. Digital work orders can be tracked, created, and assigned digitally. Work order software helps automate the fleet maintenance process via tracking service and creating work orders.
Utilize Inspection Results
As soon as a vehicle fails an inspection item, it starts generating expensive downtime. Work order software lets managers conduct digital inspections. Users can efficiently create work orders based on which inspection items fail.
When fleets have an efficient workflow from inspection results to work order generation, they can take action on issues immediately. It doesn’t matter if your fleet performs maintenance in-house or outsources it to a third party — work order software can help you create work orders quickly to get your vehicles back on the road as soon as possible.
Fleet managers who streamline maintenance management by optimizing vehicle work orders will benefit from reduced vehicle downtime and a greater understanding of fleet operation costs. To learn more about fleet optimization and saving your team money, visit Azuga.