We’ve been warned about a driver shortage and a technician shortage in the fleet tracking industry for several decades now.
Some questions:
- Is this shortage really so alarming?
- What can we do about it?
- Do some companies face it more than others?
- How are new vehicles and new technologies such as fleet tracking solutions addressing the situation to an extent?
- What can you do locally, at least?
Surmounting the Crisis in Fleet Management
First, let’s take a quick look at some of the numbers that caused worry.
The US Labor Department stats on technicians (referring here to truck and bus mechanics and diesel engine specialists) referred in 2012 to how the industry would need to add over 20,000 technicians over a decade in addition to replacing about 50,000. Two years later, though about 13,000 new technicians had already joined the workforce, they revised the number of new technicians needed over the coming decade to over 30,000. Many saw the supply gap widening rapidly. From other sources, the supply gap was even more expansive. A report from TechForce said the demand for entrant auto technicians for the 2016-2026 decade was 75,900.
Today’s numbers are just as problematic. The Journal of Commerce says the “year-over-year shortfall is greater than the 59,000-driver shortage claimed by the American Trucking Associations in 2019. If the shortfall persists, 2020 will be the first year since the 2008–09 recession when the number of truck drivers dropped year over year.”
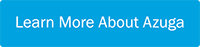
What can be done about it? Locally?
How is the demand to be addressed? Stats show that 11,000 medium- to heavy-duty truck technicians graduate annually in the U.S. from the post-secondary level. Overall, the feeling is that there are enough training establishments. Still, the industry has to figure out how to work with them instead of just holding opinions about new drivers’ competence and work-readiness. Many companies do not have an organized method for onboarding them and helping them find their bearings and settle in. This lack is usually a reason for young recruits to try elsewhere almost immediately.
Another area to address is that of managing the expectations of new entrants. Educators have to advise their students that they would have to work their way up and that they were unlikely to be assigned to engine repair in their first month at work. Managers from the truck industry have to connect more often with educators in technician schools and understand what’s going on to close these gaps. This collaboration also works via initiatives through local trucking associations.
High-Tech, Like GPS Fleet Management, Is What It’ll Take.
Vehicle technology is getting more sophisticated, and to attract more competent young people, the image of the role would need a revamp. There’s a call for the trucking industry to share in creating public messaging that projects a vehicle tech career as one that’s challenging and satisfying.
Fleet managers, familiar with fleet tracking solutions, actively consider safety innovations such as Dashcams in trucks and DTC diagnostic alerts from OBDII devices as a preventive measure to reduce crashes and downtime. They gain efficiencies by using an automated diagnostic system that translates multiple Diagnostic Trouble Codes (DTC) occurrences at once and which provides comprehensive maintenance data. Such a virtual mechanic offers an assessment of the trigger of the Check Engine Light. It then recommends that the vehicle either go in for immediate repair or schedule a check-up at the earliest convenience. This type of diagnostic help allows fleet managers concerned about fleet safety and productivity to make decisions more effectively by deploying comprehensive GPS Fleet Management solutions.
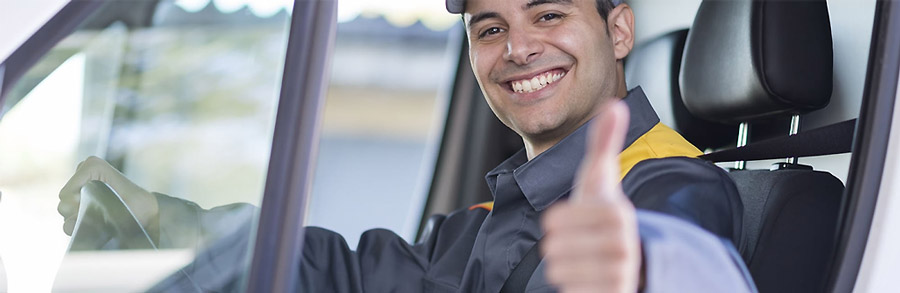
Your retention is as good as your telematics-based rewards program
According to Commercial Carrier Journal, the annualized turnover rate for large trucking companies is 92%, 72% for smaller truckload carriers. FleetCardsUSA estimates that turnover for a single driver can cost up to $15,000, meaning an annual expense of $2.8 billion across the trucking industry. Meanwhile, industry experts once said that by 2024, there would be a supply gap of 175,000 truck drivers. They said this when miles per truck were recovering after a steady fall in freight over five years when average truck miles per month had declined by about 25%.
Another strong indicator of a Driver shortage since 2014 is a shorter gap between two rounds of pay raises. Characteristically in the trucking industry, an industry-wide rise in pay takes about three years. An enterprise fleet company initiates the raise, and over several months, many other large companies follow suit. Since this gap got halved during 2014, it was a clear sign of a mounting shortfall.
The pragmatic answer to this lies in building a work culture that combines work management features (such as job forms and time cards) with rewards-driven telematics. Azuga has done trailblazing work that offers complete driver transparency, comprehensive driver scorecards, and one-click rewards for top drivers.
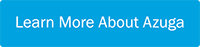
Azuga has an award-winning fleet solution used by thousands of businesses—from the small fleet of a few vehicles up to several thousand—and lauded by our GPS Fleet Management customers for its ease-of-use, robust features, and affordable pricing.